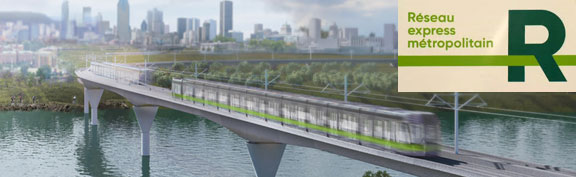
The Réseau express métropolitain (REM) project includes a total of 26 stations and span the greater Montréal area with 67 km of rail tracks. How are the elevated structure sections being manufactured? The Béton préfabriqué du Lac (BPDL) team produced 4,550 precast concrete segments representing 14.5 km of elevated structure. The specialized and meticulous work was customized according to the needs of the construction site, yet the prefabrication in the BPDL local precast concrete manufacturing plant allowed the project to move very quickly. Prefabrication also guaranteed superior quality as the components were manufactured in a highly controlled CPCQA certified precast facility. Here is a step-by-step visual presentation of how a segment is being manufactured for this project:
Step 1: Bending of the reinforcement
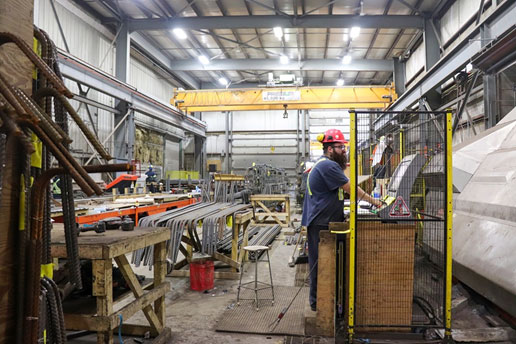
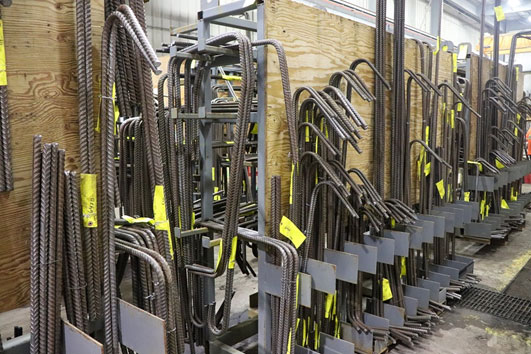
- Different steel bars were used to form the reinforcement.
- Specialized equipment was utilized to bend the steel bars at the manufacturing plant.
- After they are identified and sorted in preparation for the next phase.
Step 2: Reinforcing cages
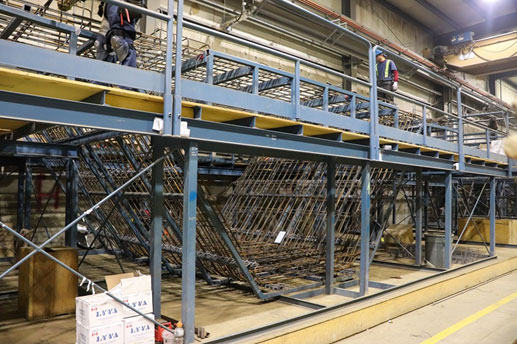
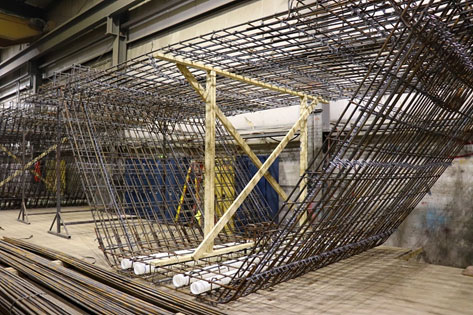
- In another part of the manufacturing plant, the assembly of the reinforcing cages begins using the bent steel bars, which were completed in the previous step.
- When this assembly is completed, the reinforcing cages are brought to a temporary storage area.
Step 3: Concreting
- After the reinforcing cages are assembled, they are placed in the mould.
- Every component is installed precisely. During this step, it is crucial to closely examine the process to ensure that the alignment is accurate.
- Match casting is used to prepare for concreting. To be sure that the alignment is absolutely perfect, the segments are concreted against the former segment.
Step 4: Precast Concreting of segments
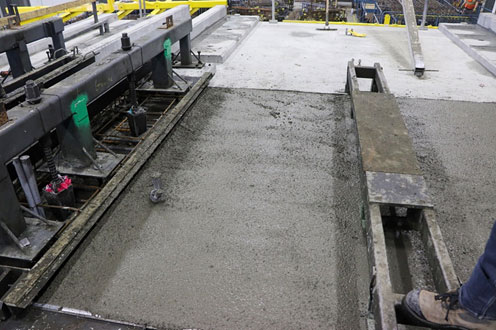
- Once it is finalized and ready, the segments are concreted.
- Two types of segments are manufactured: typical segments and stacked segments. The stacked segments are shaped differently since they will rest on the pillars of the aerial structure.
- As illustrated above, each segment is concreted right on the previous segment (match casting).
- The formwork is completed about 12 hours later. In order to separate the two segments after the operation, they use a mixture of soap and talcum powder.
Step 5: Finishing process
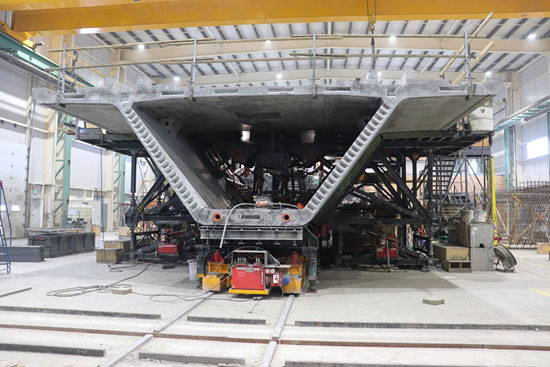
- After the concreting is finalized, the segment is relocated to another section of the plant to proceed with the finishing, which includes grinding the finish, cleaning the surface used for match casting and also fixing any minor defects.
Step 6: Cooling and Step 7: Storage
- Once the finishing process is completed, the segment is moved to another section of the plant where it will sit for roughly 8 hours to cool down.
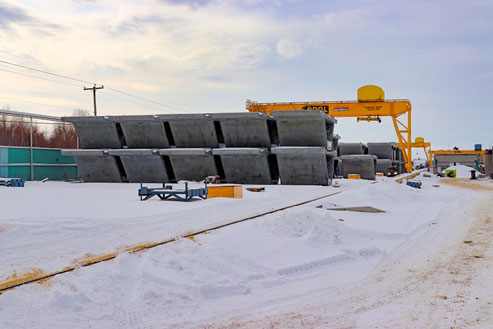
- The segments are stored outside. They will remain in the yard until they are shipped to the construction site.
- They are transported to the West Island, where they will be assembled to form the elevated structure for the Réseau express métropolitain.
Project highlights
- A total of 4,550 segments will be prefabricated over three and half years
- This is the equivalent of 14.5 km of the elevated structure
- Since January 2020, 1,400 segments have been completed
- The manufacturing plant produces an average of 34 segments weekly (28 typical segments and 6 stacked segments)
The REM project greatly benefits from the expertise and experience of the BPDL team. BPDL has been involved in other major projects in Montreal such as the new Champlain Bridge and the Turcot Interchange.
Consortia
Infrastructure engineering, procurement and construction (EPC)
Groupe NouvLR
- Members: SNC-Lavalin, Dragados Canada Inc., Groupe Aecon Québec Ltée, Pomerleau Inc., EBC Inc.
- Participants (NouvLR Conception): SNC-Lavalin, Aecom Consultants Inc.
- Architecture: Lemay, Bisson Fortin, Perkins + Will, Provencher Roy